Toyota Production System (TPS)
TPS (Grade IV) Certificate Program
By TMS TPS Certificate Institute & Toyota Engineering Corporation – Japan
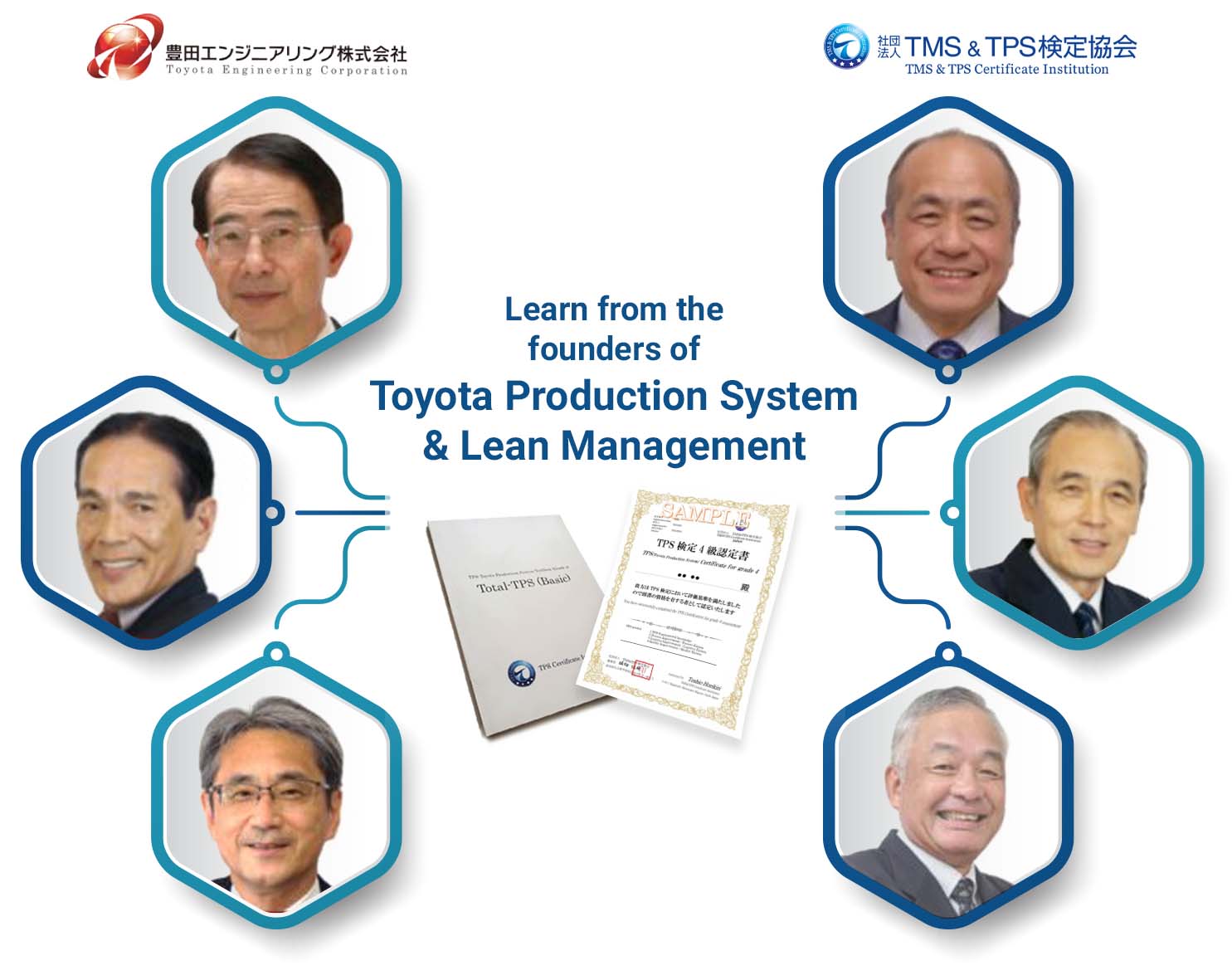
About Toyota Production System (TPS - Grade IV) Certificate Program
Toyota Production System (TPS) is considered as the world’s most successful strategy for operational excellence. This methodology was born, raised and evolved at Toyota Motor Corporation in Japan for seven decades and is now being used as a strategic weapon for businesses, governments, and institutes around the world.
Toyota Engineering Corporation (TEC) was established in early 2000 to popularize the Total Toyota Production System or Lean Management across the world. Currently, they have certified more than 13000 professionals across the globe. The Senseis at TEC possess decades of hands-on experience in developing, sustaining, and improving TPS management concepts at Toyota and affiliated companies
TPS certification provides the most authentic, up to date, practical knowledge and application on Toyota Production System. TPS Level IV certification is an essential step for manufacturing leaders to develop “must-know” practical skills in Toyota Production System
BEST FOR
Leaders in the manufacturing sector
DELIVERY
Online (ZOOM) | 24 Hours | 6 Saturdays
MATERIAL
TPS Text book
MODE
Instructor-led training (Executive TPS Sensei)
CERTIFICATE
Printed & Digital Certificates from TMS TPS Certificate Institute- Japan
Upcoming Programs 2025/26
Find the program itinerary for the upcoming programs.
- Introduction - 19th July 2025
- Session 01 - 26th July 2025
- Session 02 - 2nd Aug 2025
- Session 03 - 9th Aug 2025
- Session 04 - 30th Aug 2025
- Session 05 - 6th Sep 2025
- Examination - 20th sep 2025
- Introduction - 15th Nov 2025
- Session 01 - 22nd Nov 2025
- Session 02 - 29th Dec 2025
- Session 03 - 6th Dec 2025
- Session 04 - 13th Dec 2025
- Session 05 - 10th Jan 2026
- Examination - 24th Jan 2026
Congratulations to the Graduates of the Previous Batch (March 2025)
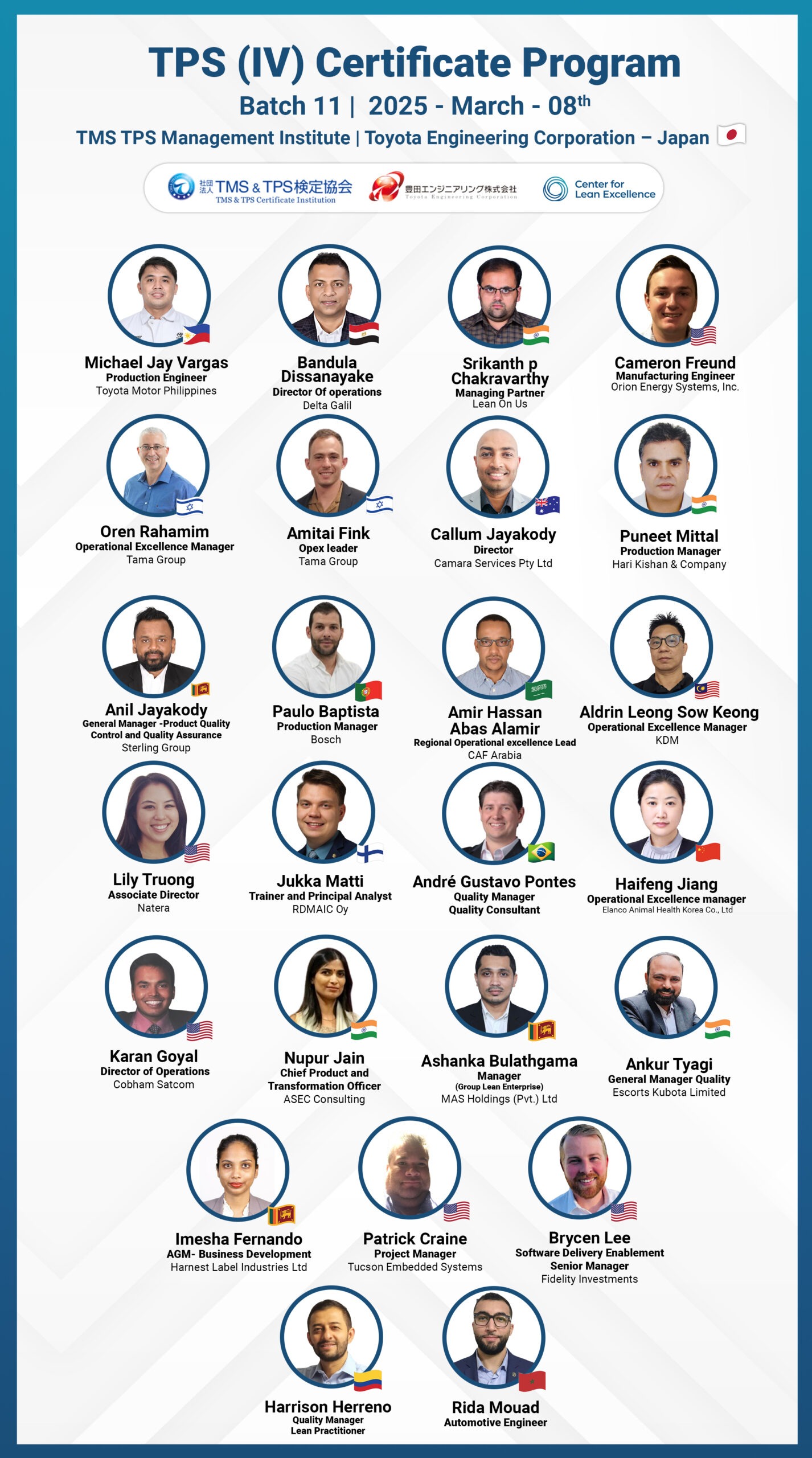
It was a true honor to witness such an inspiring and diverse group of professionals complete the TPS Certificate Program. Over the course of the program, each of you demonstrated exceptional commitment to excellence, Lean thinking, and continuous improvement.
🌏 Congratulations to:
🇵🇭 Michael Jay Vargas
🇱🇰 Bandula Dissanayake
🇮🇳 Srikanth P Chakravarthy
🇺🇸 Cameron Freund
🇮🇱 Oren Rahamim
🇮🇱 Amitai Fink
🇦🇺 Callum Jayakody
🇮🇳 Puneet Mittal
🇱🇰 Anil Jayakody
🇵🇹 Paulo Baptista
🇸🇦 Amir Hassan Abas Alamir
🇲🇾 Aldrin Leong Sow Keong
🇺🇸 Lily Truong
🇫🇮 Jukka Matti
🇧🇷 André Gustavo Pontes
🇨🇳 Haifeng Jiang
🇺🇸 Karan Goyal
🇮🇳 Nupur Jain
🇱🇰 Ashanka Bulathgama
🇮🇳 Ankur Tyagi
🇱🇰 Imesha Fernando
🇺🇸 Patrick Craine
🇺🇸 Brycen Lee
🇨🇴 Harrison Herreno
🇲🇦 Rida Mouad
👏 Well done, everyone! The Lean journey continues, and we are proud to walk this path with you.
TPS Grade IV Program Content
- Introduction and Warm up Session
- Getting to know about TPS Program and it’s struture
- Explanation of TPS Vocabulary
- Things to know about the TPS session and the final examination
- Introduction to Toyota Production System (Lean Management), Just In Time & Jidoka
- The background of lean management and TPS
- Sharing value within the company
- Introduction to pull production
- The concept of JIDOKA
- Big lot production & Small lot production
- Q&A
- Implantation of Total TPS
- Revitalizing workplace
- i. QC circle activity
ii. Multiskilled development (job rotation)
iii. Creative idea suggestion system
iv. Safety and health in workplace
v. Equipment maintenance
vi. Product quality
vii. Production division council
viii. Roles of supervisors
ix. Human resources development
x. Enhancement of welfare facility
- i. QC circle activity
- Participation and improvement of workplace
- 5S (4S and 1S) in workplace
- Visual control in the workplace
- Preparation of operation standards
- Operation Kaizen
- Establishment of standardized work
- Elimination of MUDA
- Reallocation of work
- Productivity (Work efficiency)
- Actual kaizen in process (lead-time reduction)
- Logistic Kaizen
- Part receiving
- Material handling in plant
- Kanban system
- Q&A
- Equipment Kaizen
- 5S of equipment
- Equipment maintenance
- Quality Kaizen
- Quality built in process
- Development of quality assurance mechanism
- QC network
- Quality assurance in process
- Quality assurance in purchasing parts
- Advanced Kaizen (New Product Introduction)
- SE (Simultaneous Engineering Activity)
- Production Preparation activity
- Manufacturing preparation
- Quality assurance in preparation activity
- Promotion of advanced kaizen by Oobeya system
- Evaluation of company strength and TMS
- Q&A
- TPS Grade IV Examination (80 MCQs | 60 Mins)
Download Program Brochuer
Linkedin Notes from Alumni
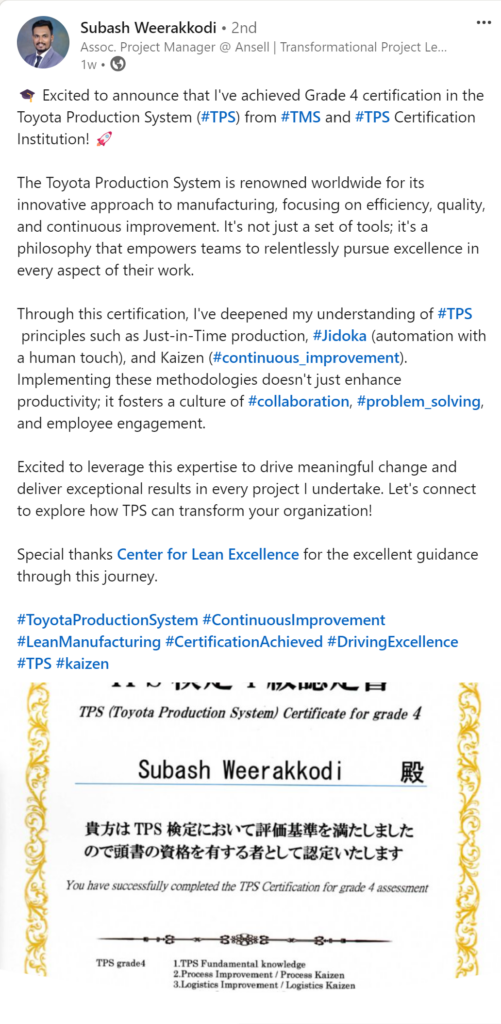
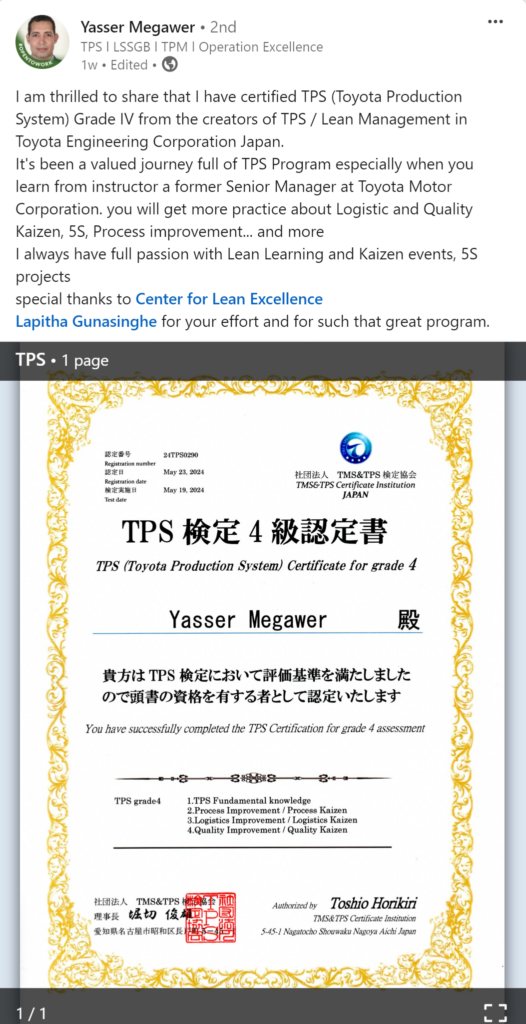
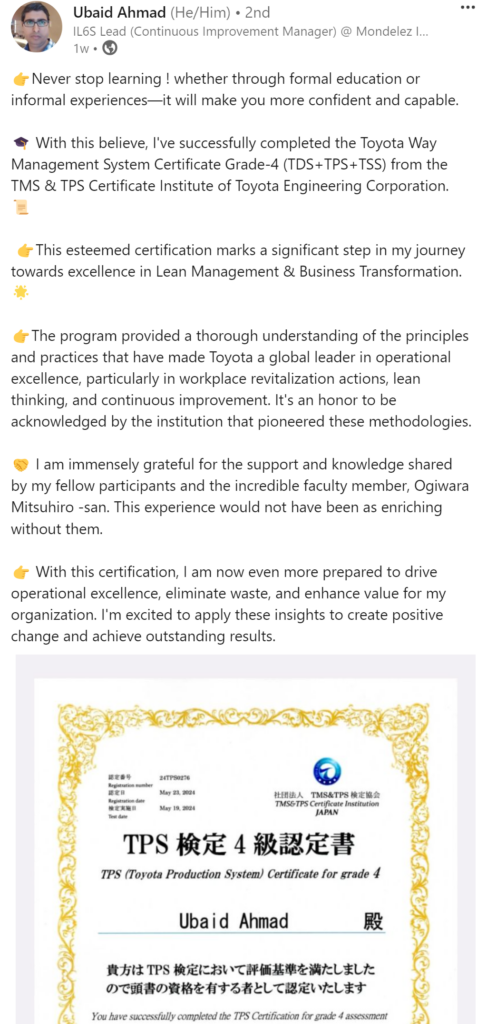
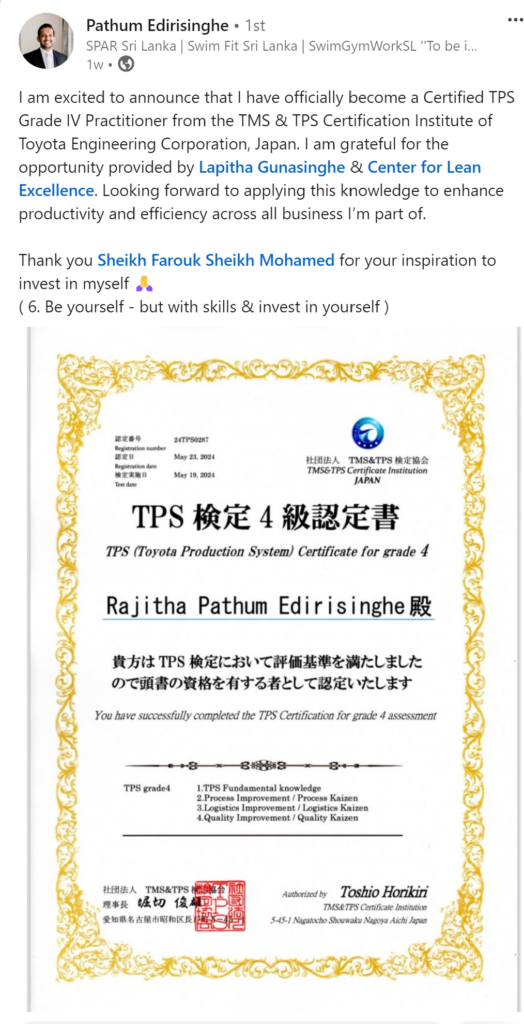
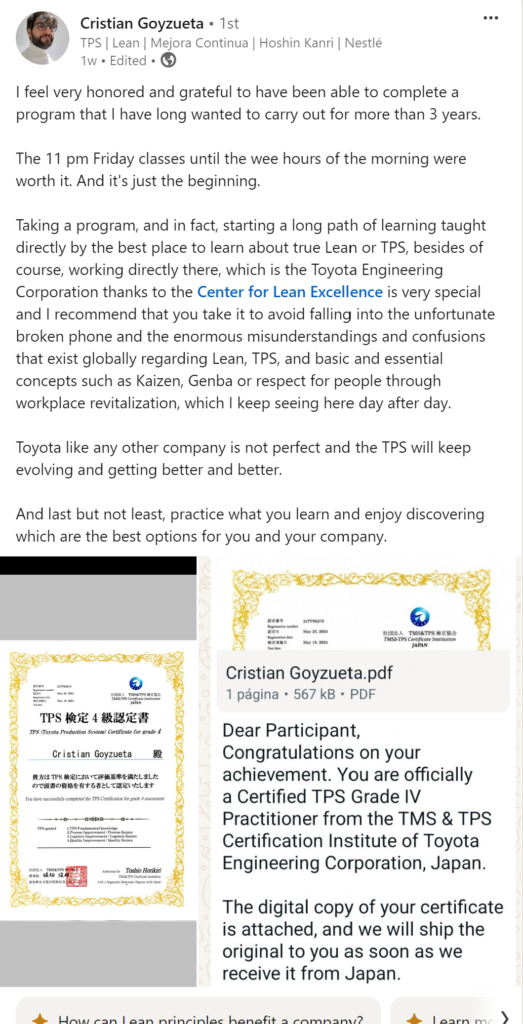
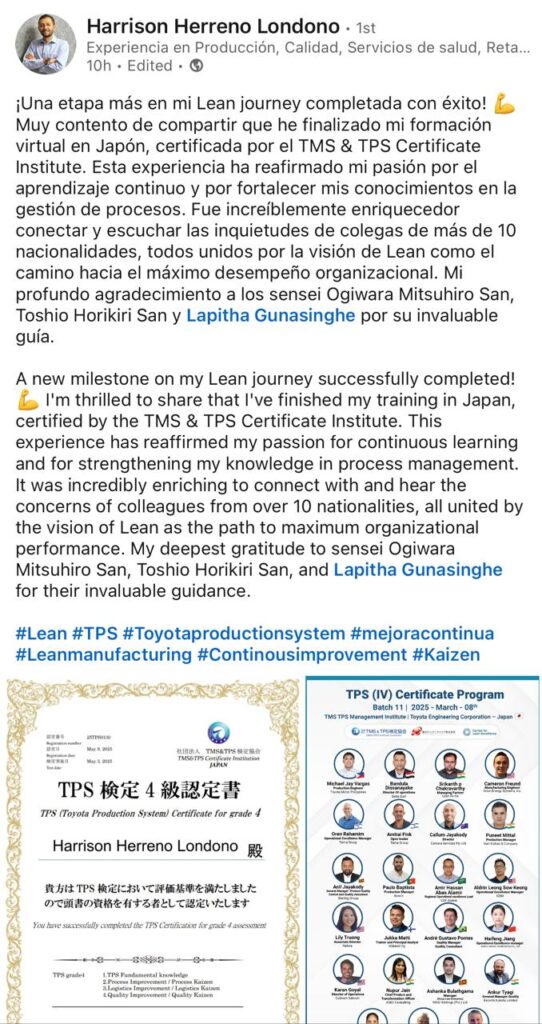
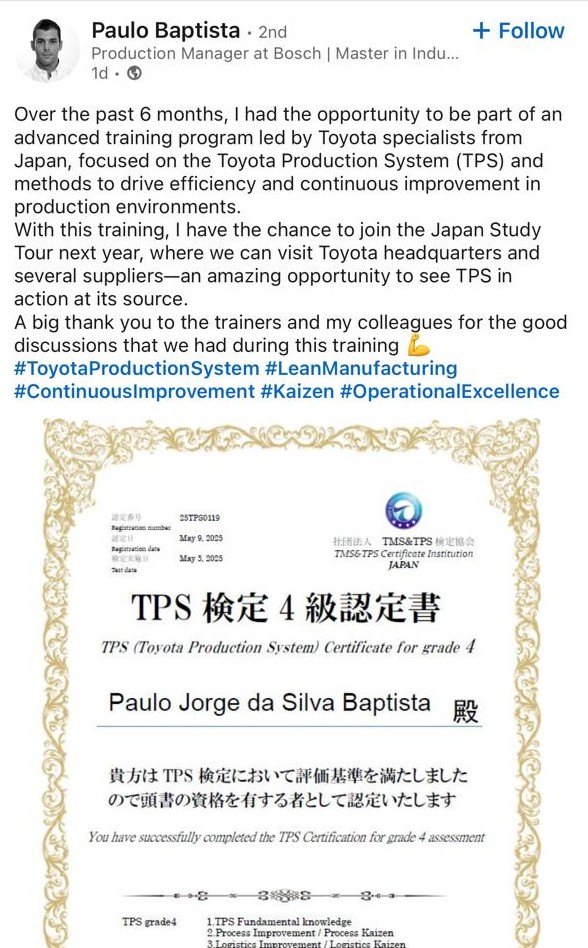
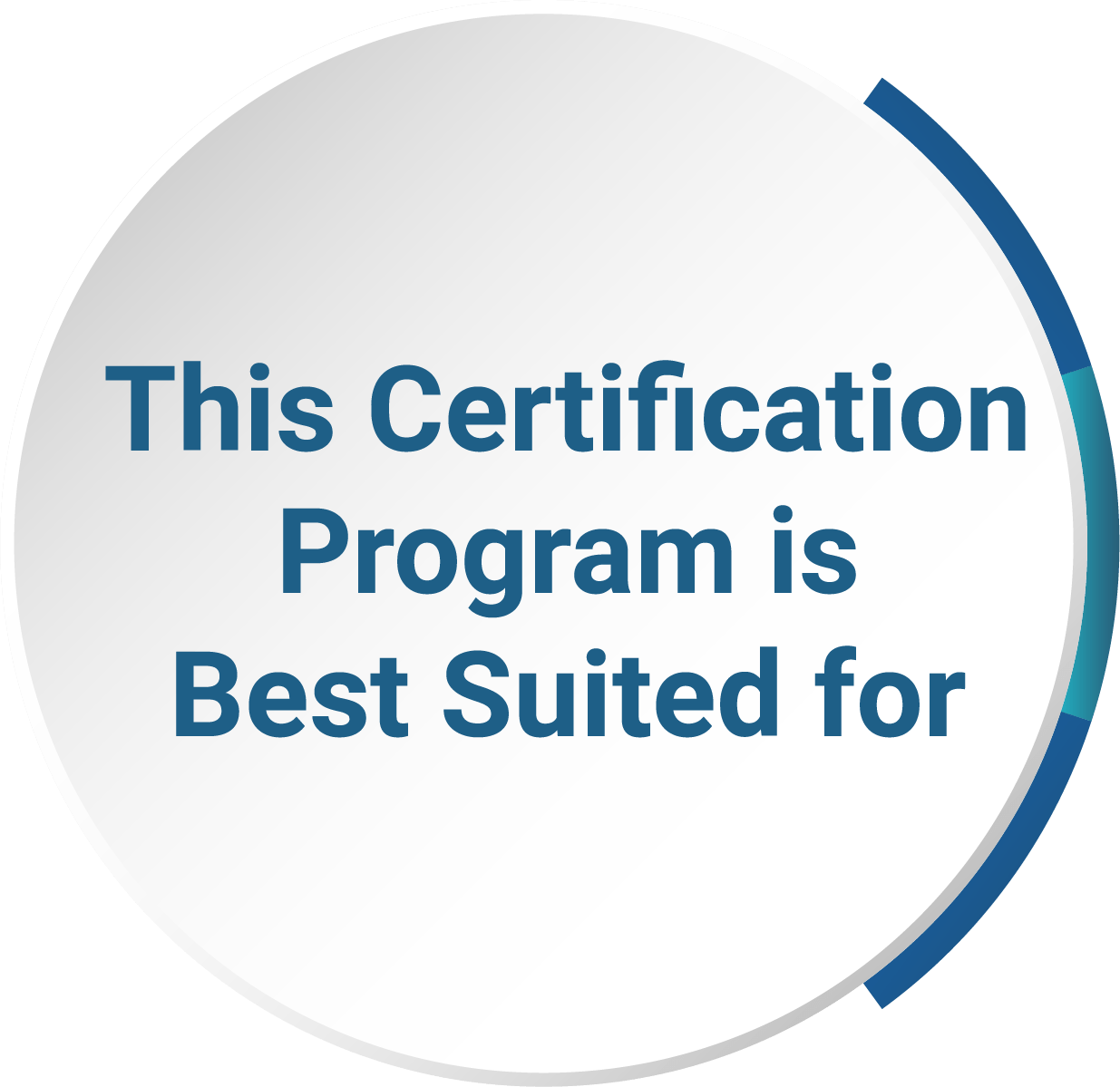
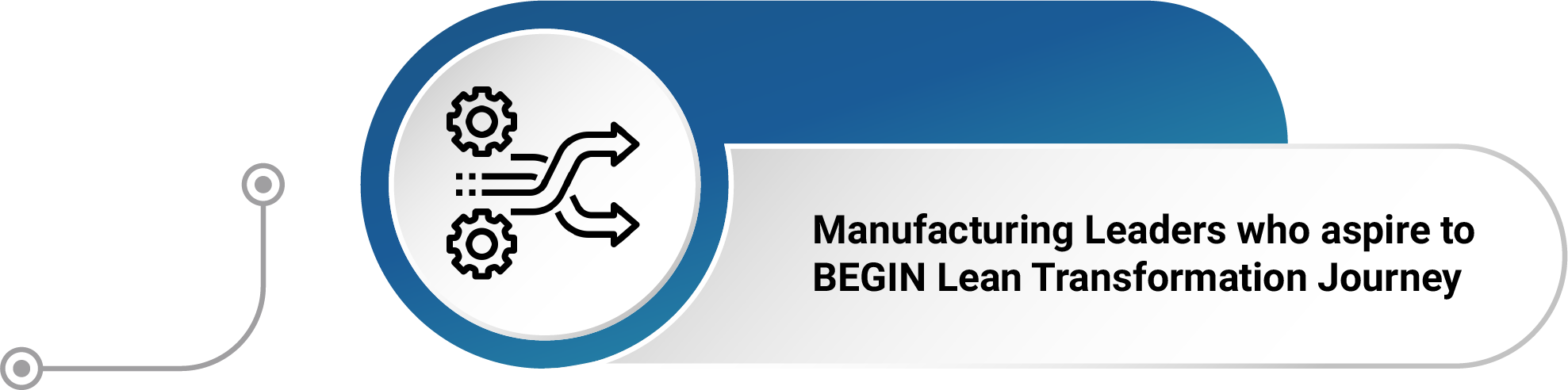
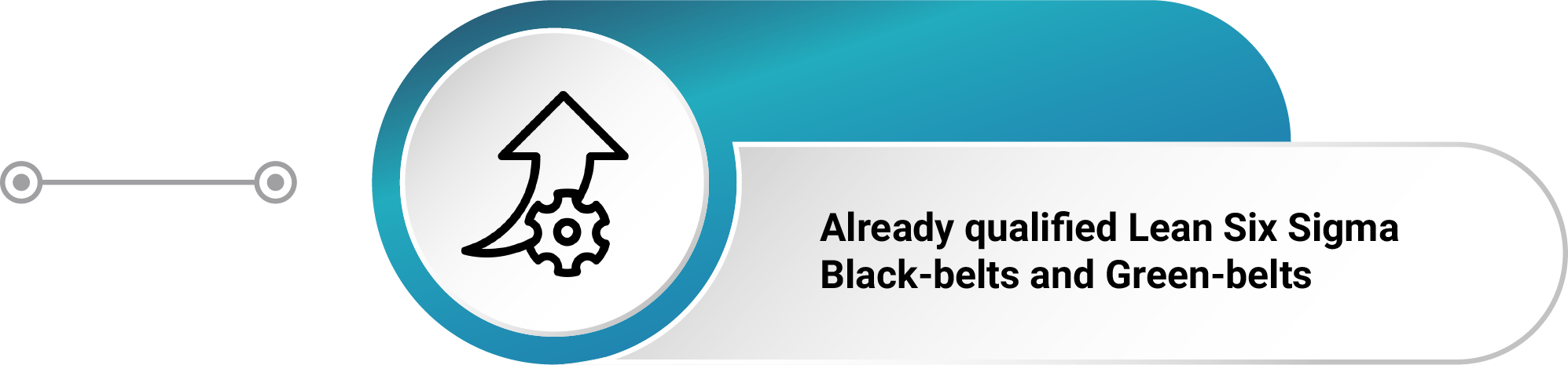
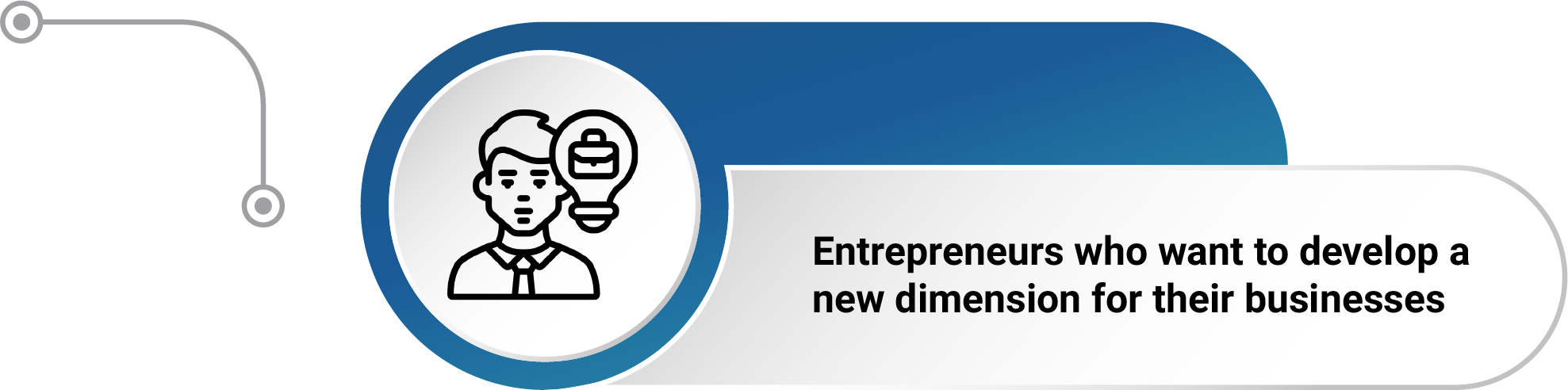
Investment
- Early bird discounts for registrations 1 month before the start date
- * Postal / Courier charges will be separately billed for overseas participants
More Seats Left
Contact us for more details:
Meet Your Sensei
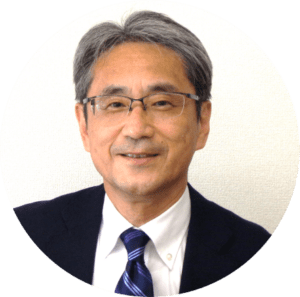
Ogiwara Mitsuhiro
Former Senior Manager with 37 Years of experience at Toyota Motor Corporation
Prestigious Certificate from Toyota Engineering Corporation
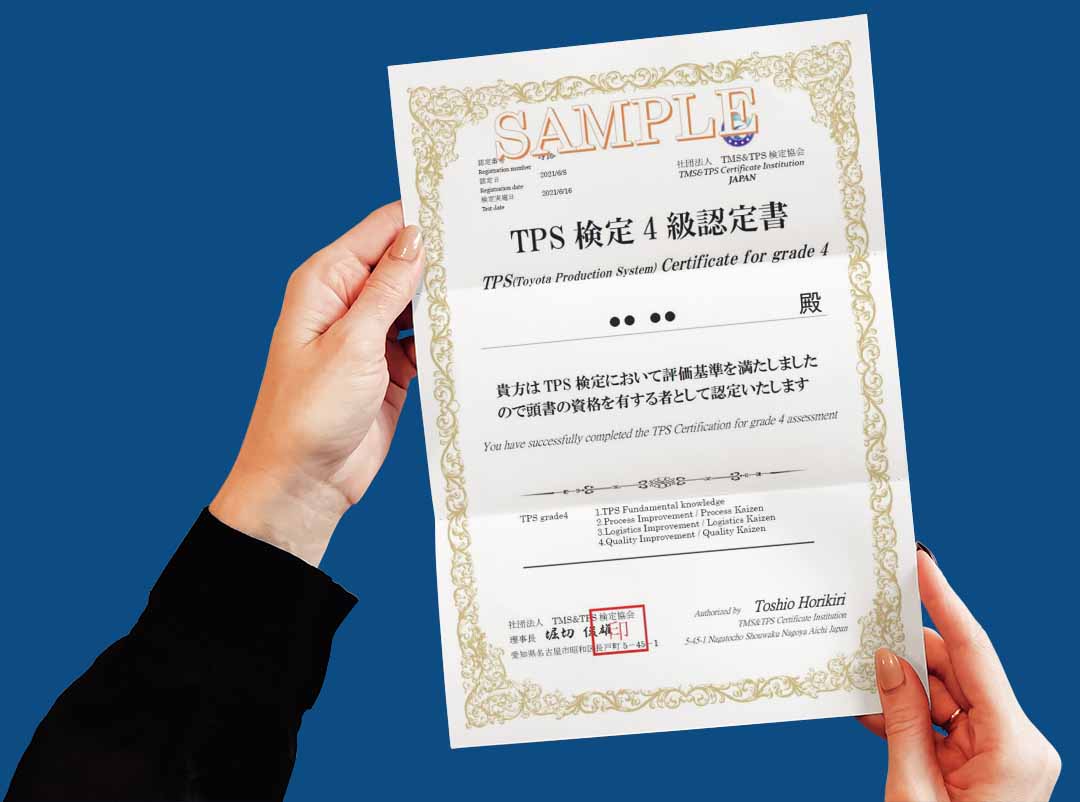
Previous Batches of Certified TPS Practitioners
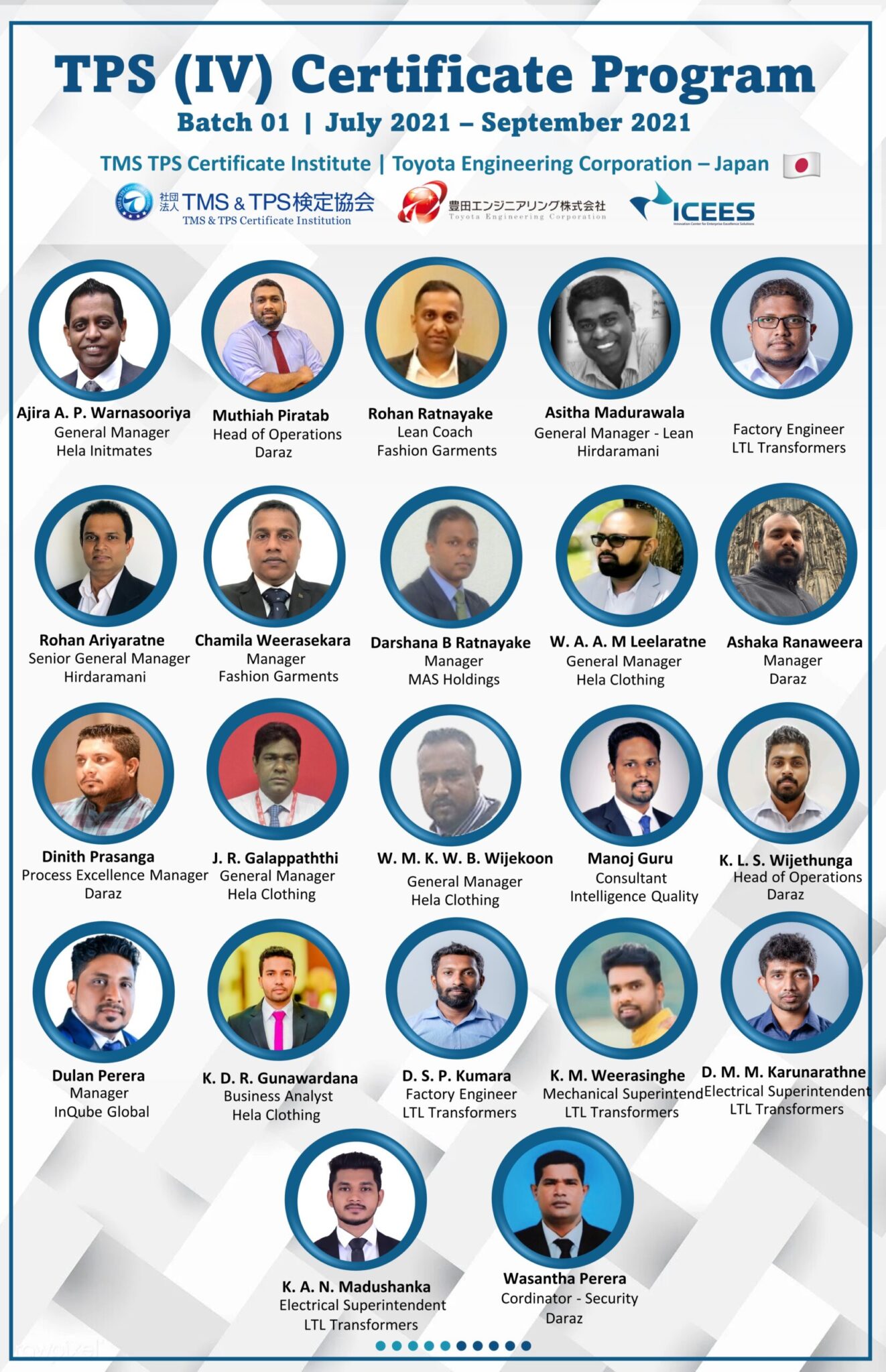
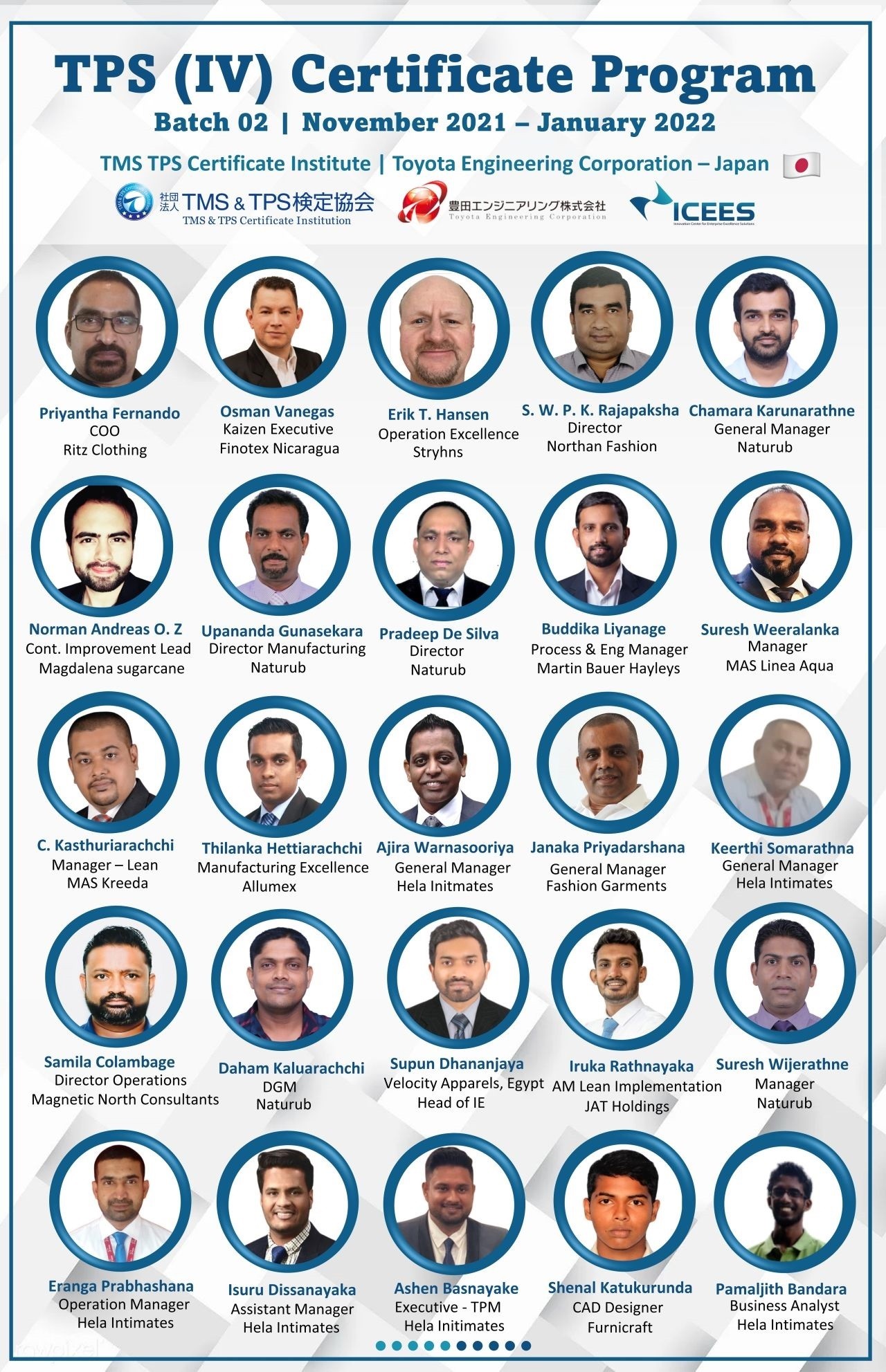
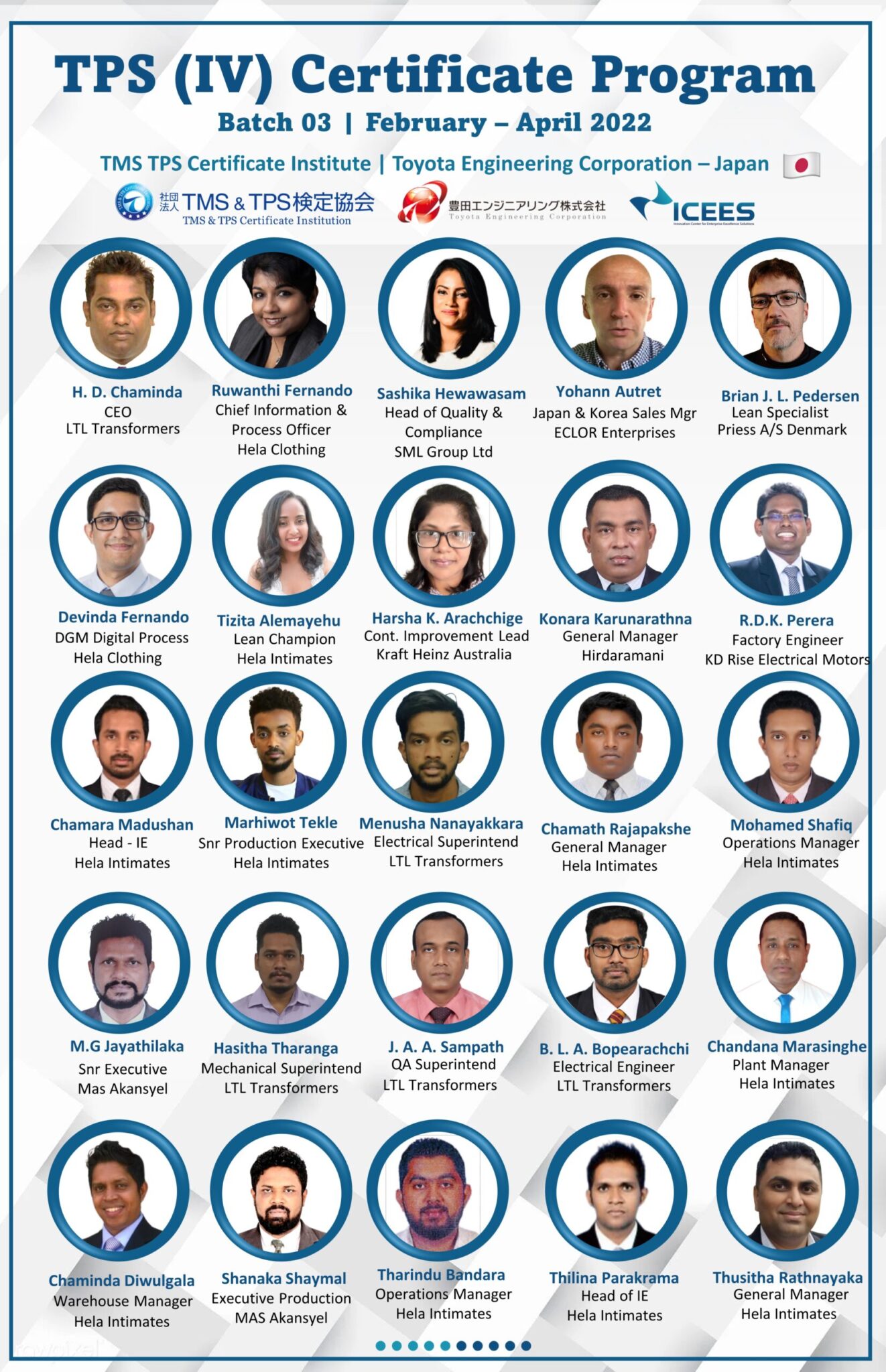
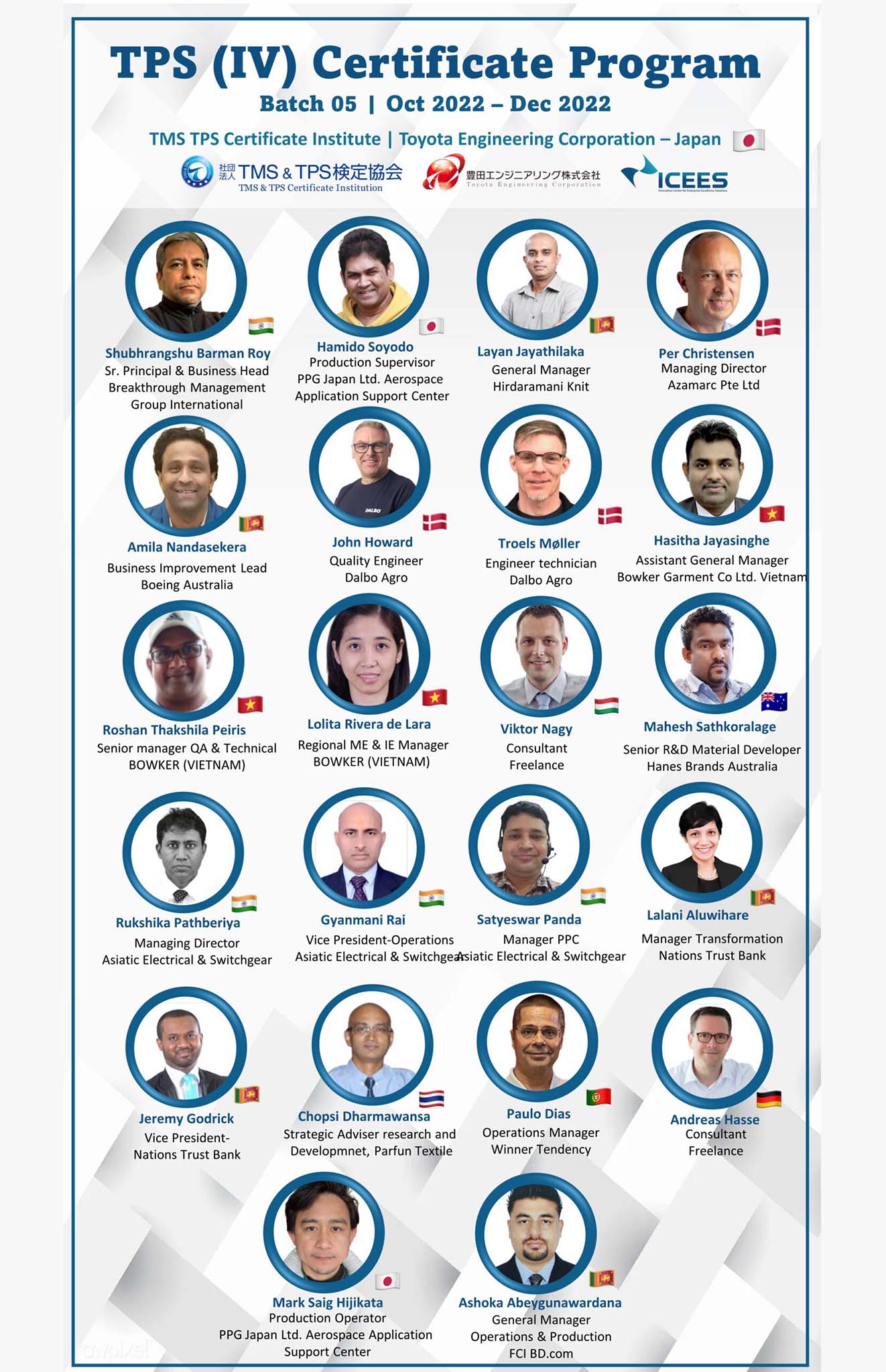
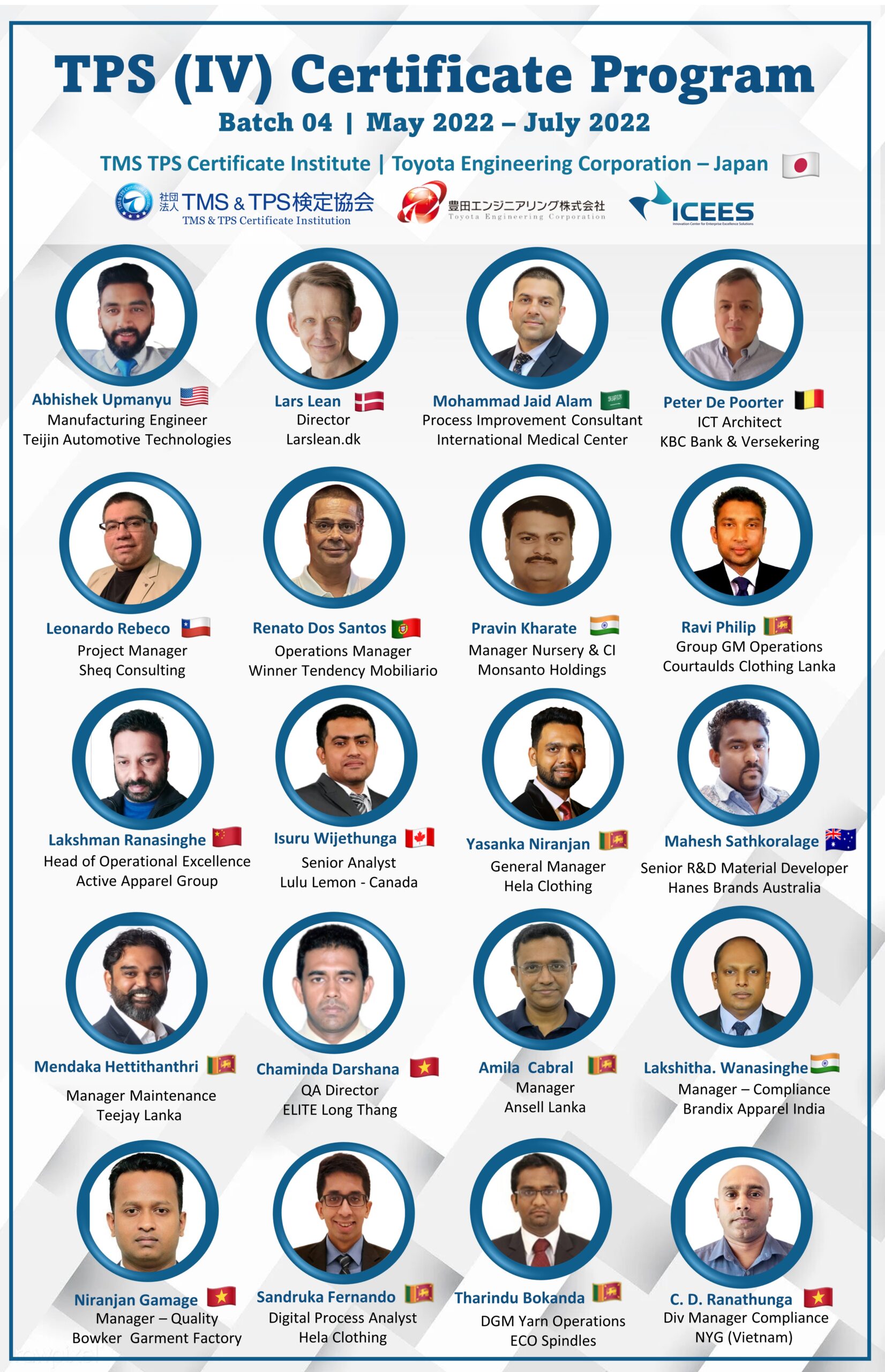
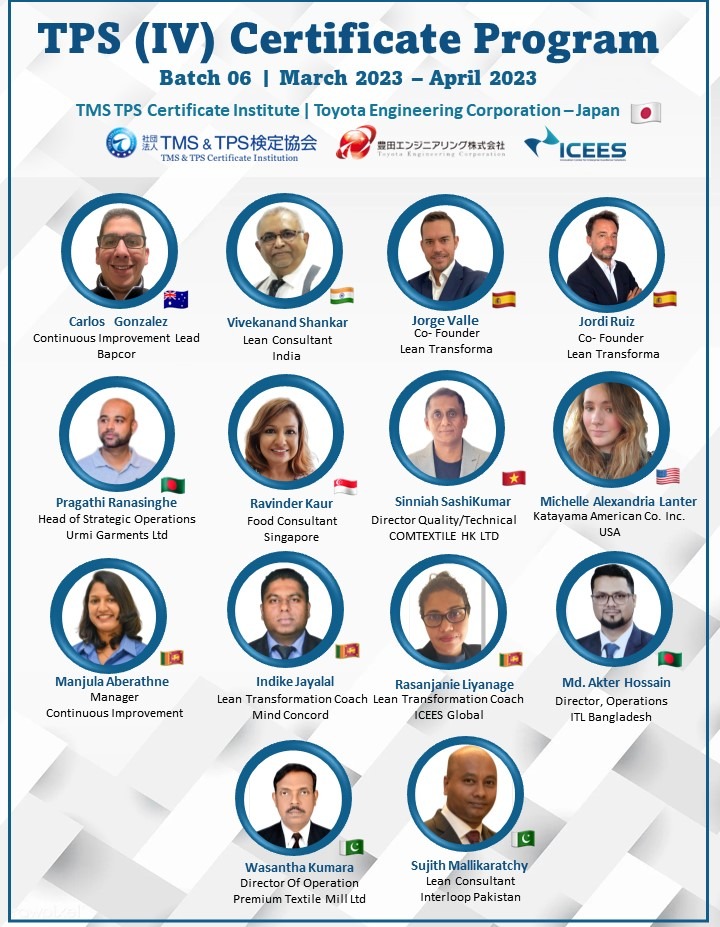
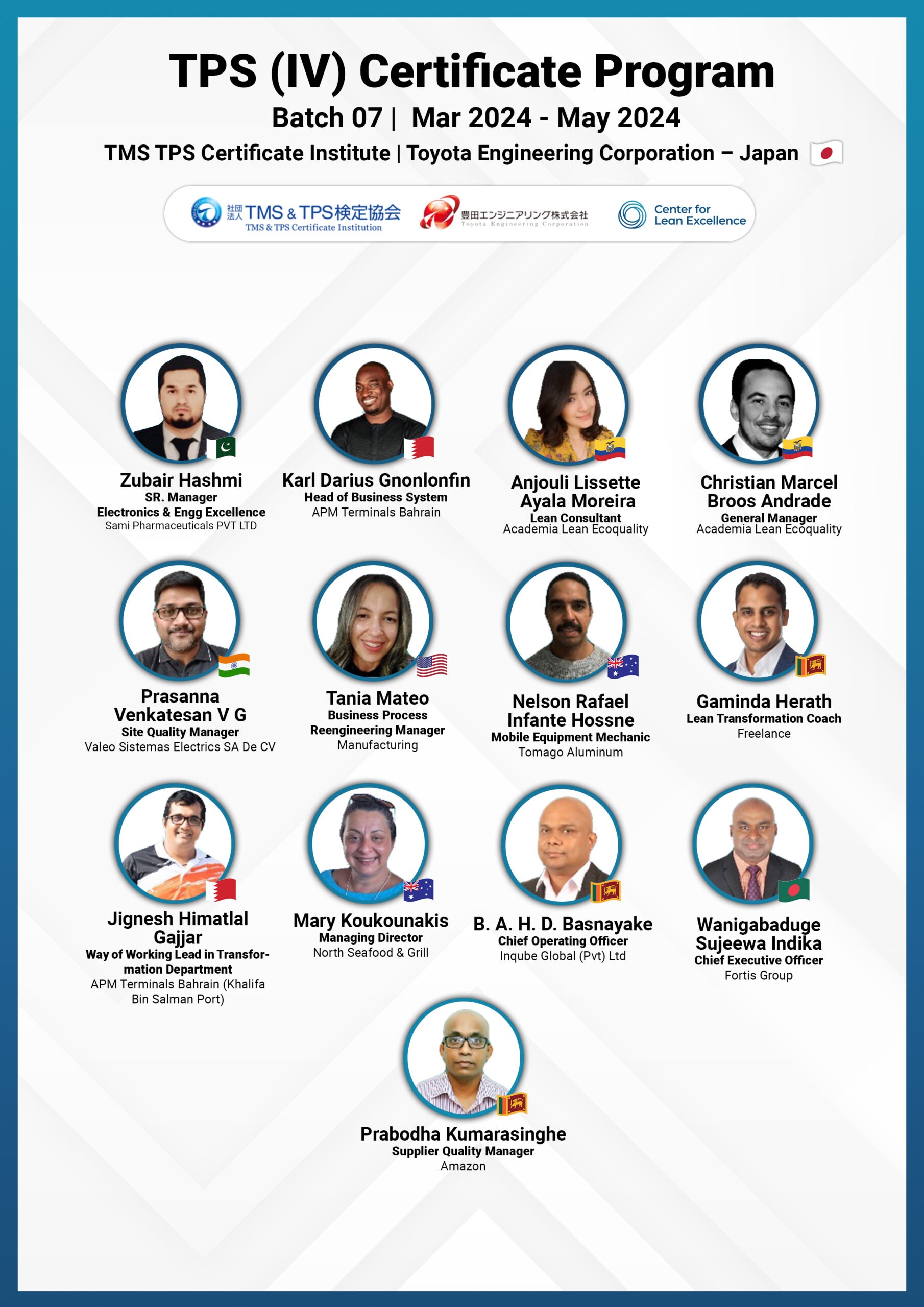
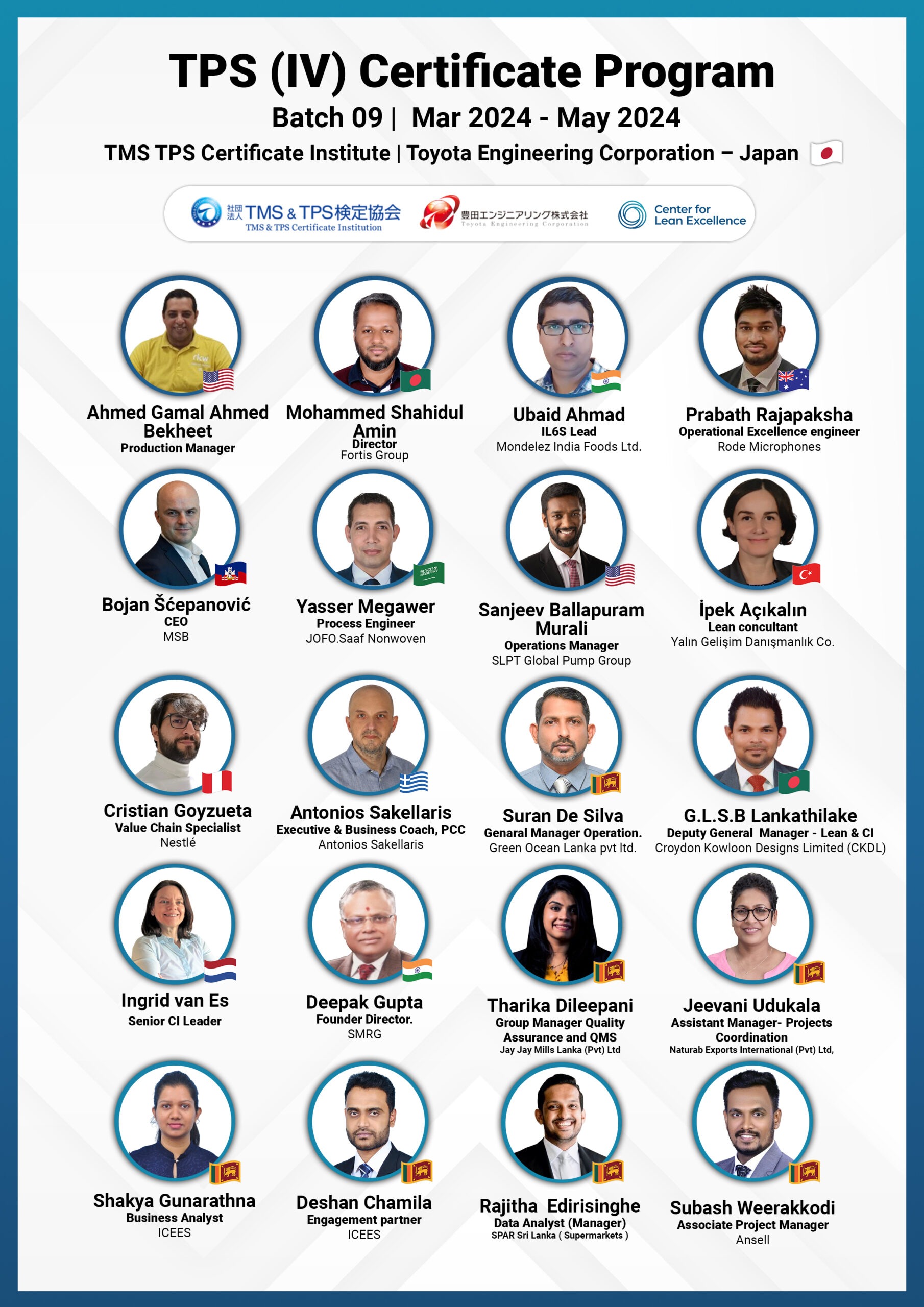
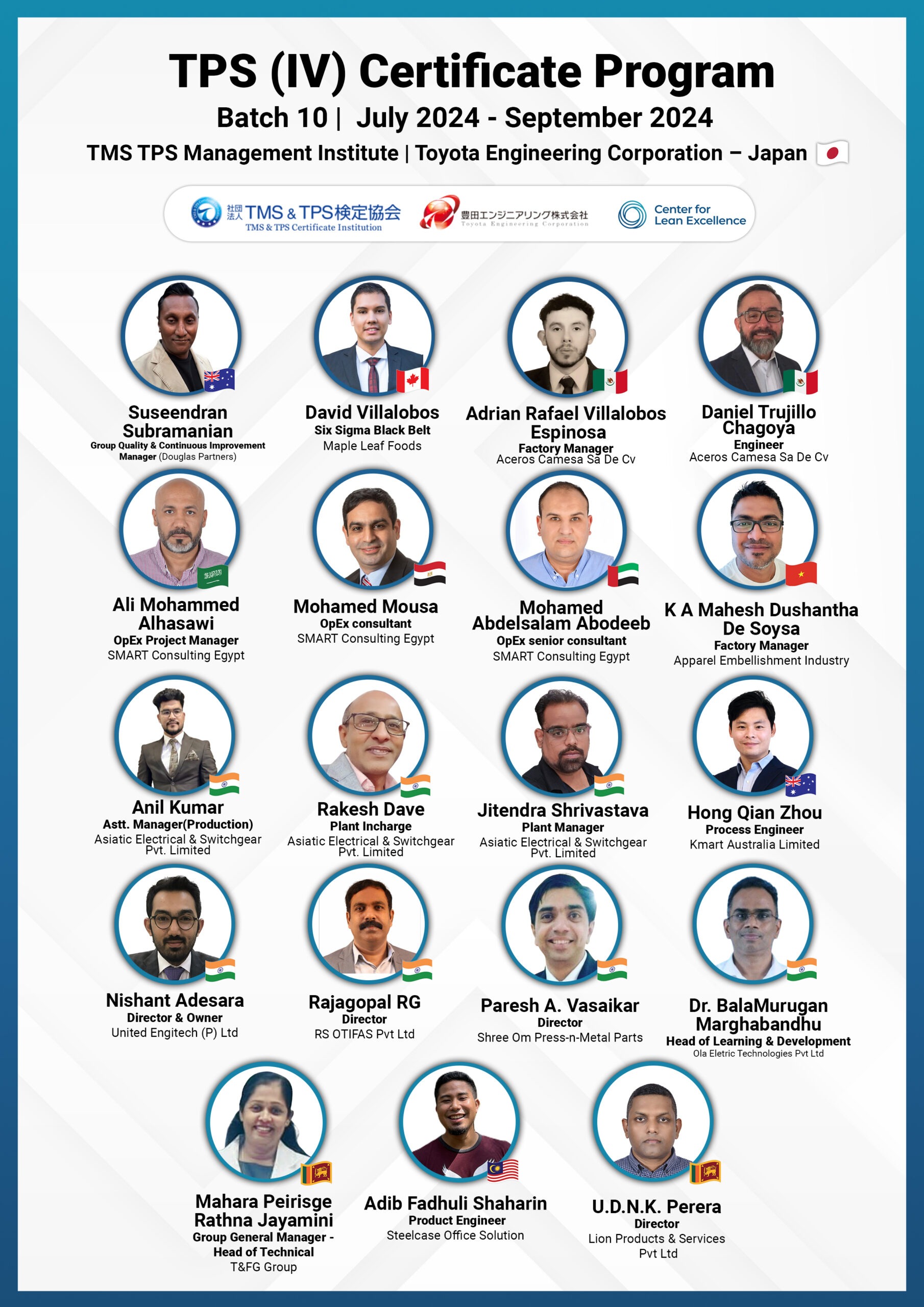
"Participating in this program helped me to get a deeper understanding of the Total Toyota Production System. Revitalization of the workplace and respect for people are two key takeaways for me. I started involving the people in my workplace in daily problem solving and was amazed at the number of kaizens that can be done on the shop floor. It was an honor to learn from Masters and the Toyota Engineering Corporation."
Brial. J.L Pederson Lean Specialist – Denmark
TPS Certification Journey
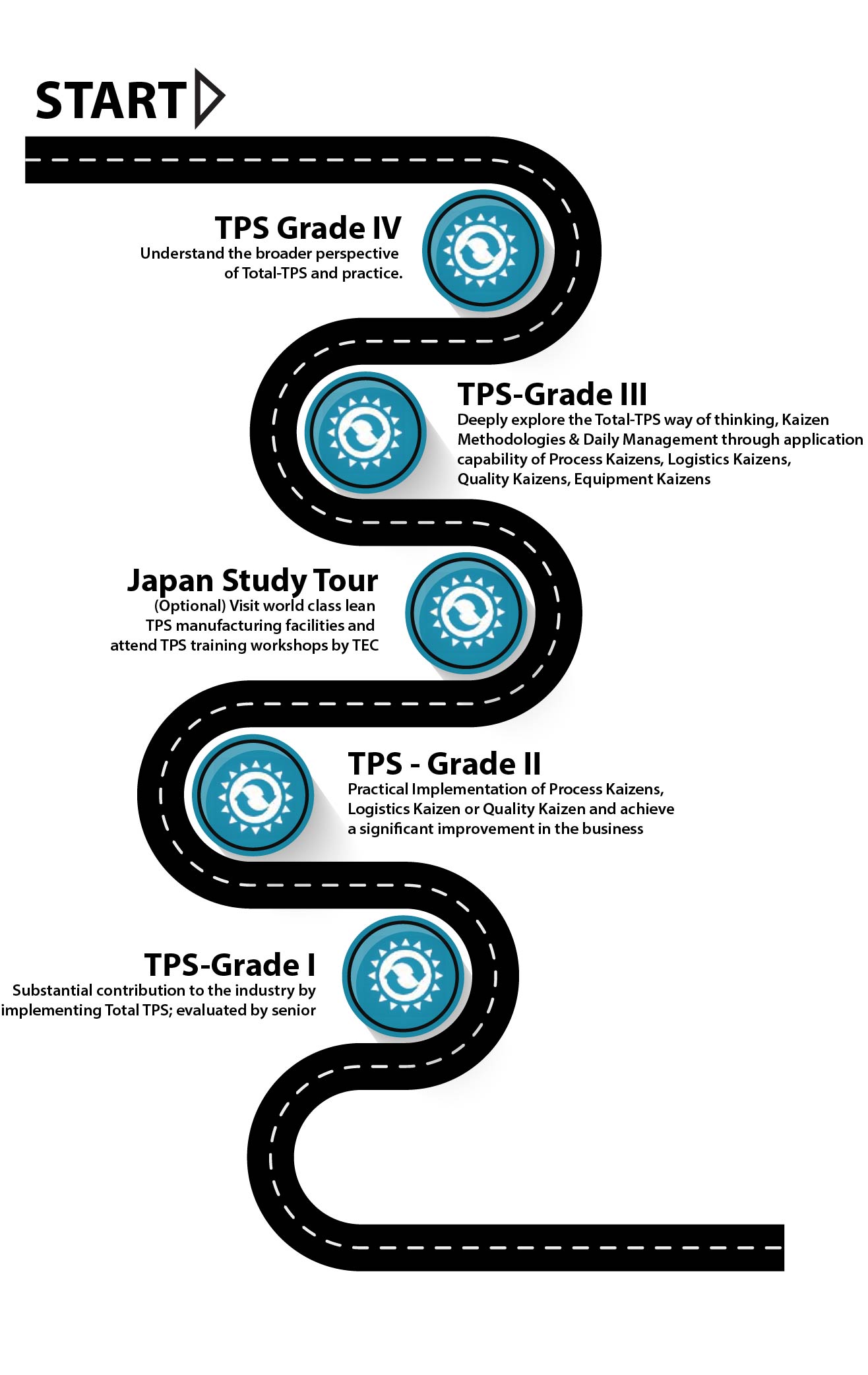
Receive Your TPS Grade IV Hand Book to Your Door-step
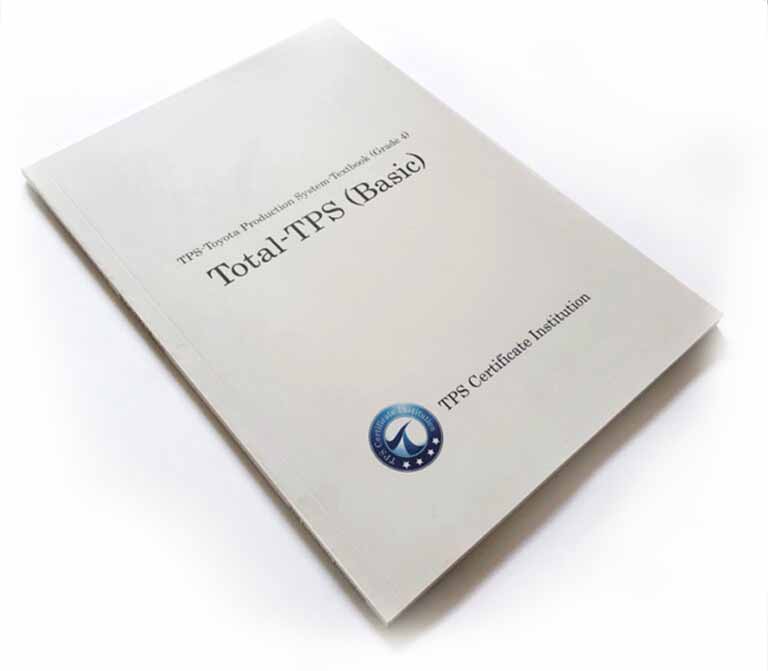