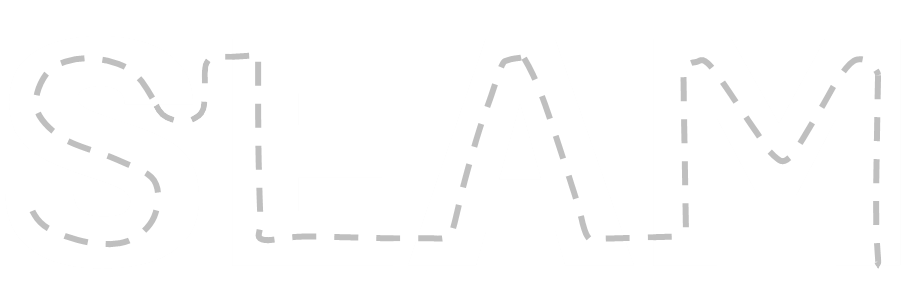
Skill Elevation in Apparel Manufacturing
Sewing | Cutting | Production | IE | Process Management
Lean Problem Solving | Kaizen | Waste Elimination | Process Mapping
Communication | Professionalism | Adaptability | Negotiation
SEAM Background
Our team comprises seasoned experts who have held senior roles in leading apparel manufacturing companies across China, India, Sri Lanka, Bangladesh, Vietnam, Jordan, Pakistan, and Cambodia. Collectively, our experts bring over 150 years of industry experience, offering invaluable insights and strategic solutions.
Since 2019, we have partnered with numerous apparel companies worldwide, helping them elevate management capabilities and enhance operational efficiency. In 2022, we became the execution partner for the GEAR (Gender Equality and Returns) program, a collaborative initiative by IFC, ILO, and Better Work Sri Lanka. Through this program, we successfully upskilled 200+ participants from 30 factories across 12 organizations in Sri Lanka. Our impact speaks for itself:
- 10,000+ training and coaching hours delivered
- 4.2% increase in operational efficiency
- 5.4% reduction in end-line defect rates
- Millions of dollars in cost savings for participating companies
- 84% of trained participants promoted within a year
Building on our extensive experience in apparel manufacturing, we are now introducing the SEAM (Skill Elevation in Apparel Manufacturing) Program—a comprehensive initiative designed to drive measurable improvements in workforce capability, efficiency, and business outcomes. Let us help your organization achieve sustainable excellence in apparel manufacturing.
SEAM Overview
Purpose
Practical, results-driven training designed to maximize efficiency in the apparel industry, addressing the gap in specialized training
Audience
Leaders, Mangers & Executives. Based on the requirement the program can be customized for Frontline Members
Training
On-Site Factory Premises. Minimum 20 participants per session. 10 Days of Face to Face Training Sessions
SEAM Scope
Technical Skill Development - 4 Days
Day | Key Area | Topics |
01 | Manufacturing Process & Role of Executive | Role of a Manager in Driving Performance |
Textile and Apparel Manufacturing Process Optimization | ||
Standard Work for Consistency and Efficiency | ||
Quick Changeover to Reduce Downtime | ||
Optimizing Layout for Smooth Workflow | ||
Line Balancing for Better Production Flow | ||
02 | Production Planning & Efficiency | Production Planning for On-Time Delivery |
Efficiency Improvement in Production Lines | ||
03 | Product Development Flow | Product Development & Pre-Production process |
Operation Cost Management for Profitability | ||
Techniques in Standard Minute Value (SMV) | ||
04 | Managing People | Skill Development for Multiskilling |
Optimizing Operator Training |
Lean Skill Development - 3 Days
Day | Key Area | Topics |
01 | Learning to See | Introduction to Lean, Value & 8 Types of Wastes |
Deep understanding wastes with process mapping | ||
Gemba Kaizen for Continuous Improvement | ||
02 | Lean Problems Solving | Structured Problem-Solving Techniques |
A3 Thinking for Project Management | ||
03 | Lean Essentials for Apparel | TPM for machine maintenance |
BIQ for quality management | ||
Pull System Kanban for flow management |
Soft Skills Improvement - 3 Days
Day | Key Area | Topics |
01 | Managing self, emotions and self-care | Managing and overcoming inner criticism and self-doubt |
Self-awareness and self-care techniques | ||
Emotional management practices | ||
Mindfulness and relaxation | ||
Stress management, self-care techniques Work-life balance | ||
02 | Personality development | Personality types |
Confidence & Positive attitude | ||
Positive personal qualities | ||
Motivation and self drive Planning and organizational skills | ||
03 | Leadership Development & Communication skills | Leadership and management styles |
Emotional intelligence Empathy, compassion and respect | ||
Effective communication skills Communication styles | ||
Presentation skills and negotiation skills |
On The Job Coaching - 2 Hours/Person
Day | Key Area | Content |
01 | Group & Individual Coaching Sessions | Observe & evaluate the trainees individually |
Identify skill gaps against the desired level | ||
Individually provide feedback | ||
Practical work shops, project monitoring and coaching. | ||
Closely monitor the personal and operational transformation |
Outward Bound Training - 1 Day
Day | Key Area | Outcomes |
01 | Full Day Outward Bound Training with Physical Activities, Games and Challenges | Managing and overcoming inner criticism and self-doubt |
Enhancing creativity, problem solving skills | ||
Increasing collaboration | ||
Resolving intra-group or personal conflicts | ||
Maintaining work-life balance with quality outcome |
Download SEAM Brochuer
Measurement & Evaluation
Operational Transformation
Baseline, Midline & Endline Progress of pilot areas - Efficiency / P2P Defect Rate & DIFOT Absenteeism / Turnover
Personal Transformation
Practical Assignment | Group Project Work | Examination | On-the-job training progress report | 360 evaluation – Before & After
Training Delivery
Post-training feedback score | Participant exam score | Individual Assignment score | Activity book completion score
Our Expert Panel
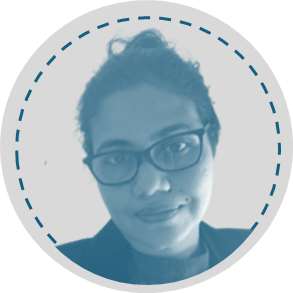
Rasanjanie Liyanage
Lead Technical Trainer | 22 Years of Experience
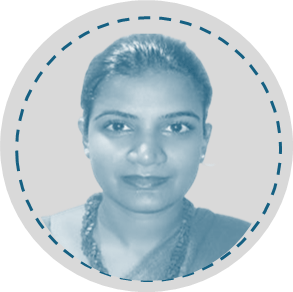
Vidarshani Perera
Lead Soft Skill Trainer | 18 Year of Experience
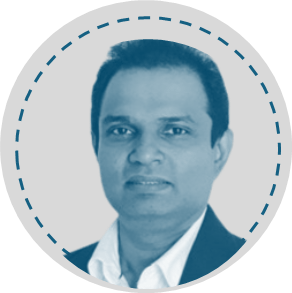
Rohan Ariyarathana
OBT Trainer | 25 Years of Experience
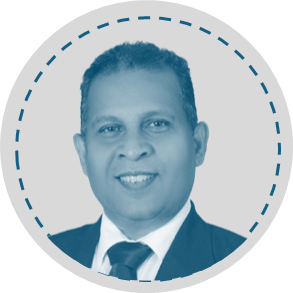
Wimal Atapattu
Leadership Coach | 30 Years of Experience
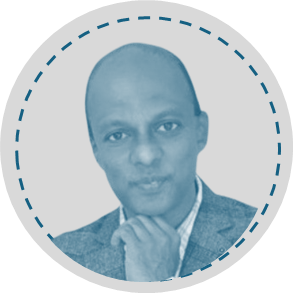
Darshana Ratnayake
Lean Coach | 25 Years of Experience
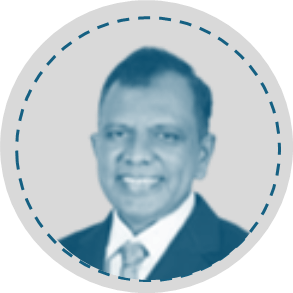
Sujeewa Waidyathilaka
Technical Skill Trainer | 26 Year of Experience
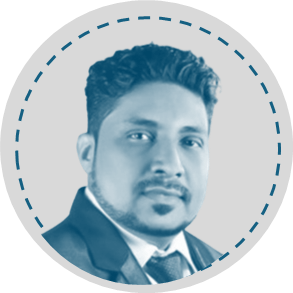
Dulan Perera
Technical Trainer | 15 years of Experience
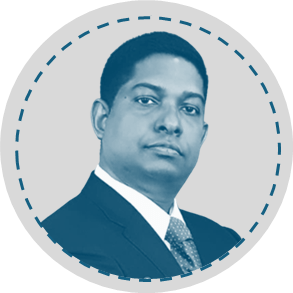
Lapitha Gunasinghe
On the Job Coach | 25 Years of Experience
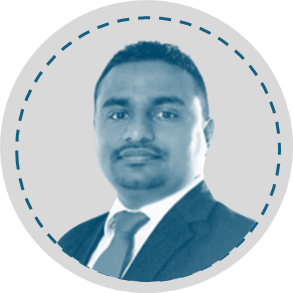
Asanka Henegedara
On the Job Coach | 15 Years of Experience
Our Impact on Sri Lankan Apparel Industry
In 2022, we became the execution partner for the GEAR (Gender Equality and Returns) program, a collaborative initiative by IFC, ILO, and Better Work Sri Lanka
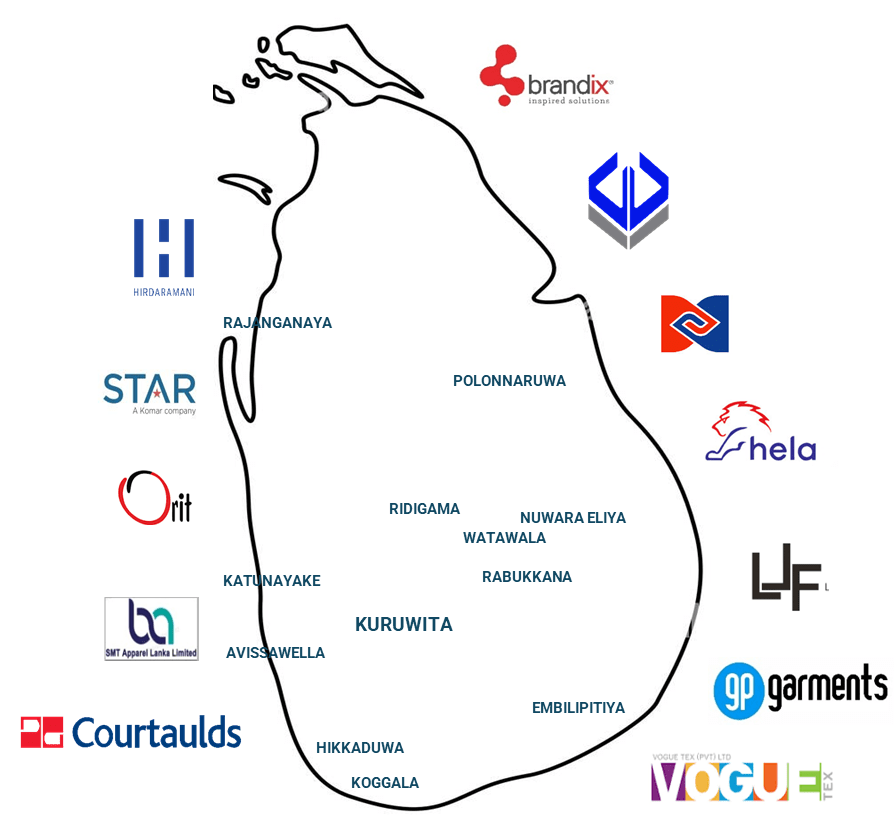
Pricing & Customization Options
In 2022, we became the execution partner for the GEAR (Gender Equality and Returns) program, a collaborative initiative by IFC, ILO, and Better Work Sri Lanka
Technical Skills Development
4 Days - USD 200 Per Person
Lean Capability Development
3 Days - USD 150 Per Person
Soft Skills Development
3 Days - USD 150 Per Person
On the Job Coaching
2 Hours - USD 250 Per Person
Outward Bound Training
1 Day - USD 150 Per Person
Notes:
- A minimum of 20 participants is required to conduct the training program.
- Airfare, accommodation, and internal transportation costs are to be borne by the client.
- Client can customize the training modules based on their specific needs.
- The client is responsible for providing the training room and necessary facilities, including a projector, whiteboards, flip charts, and other required equipment.
- Client to provide access to their factories for practical sessions.
- For OBT, the client shall provide a location that meets the specifications provided by CLE.
Book a Program for Your Company
Once you fill out the form, our team will reach out to arrange a call and discuss your requirements in detail.